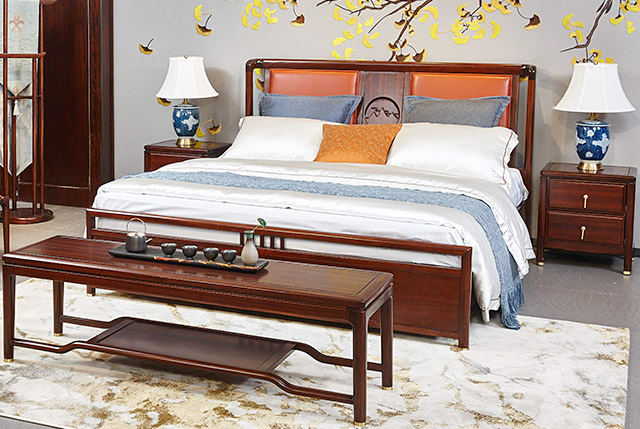
壹
居安思危,突发背后的挑战
2020疫情来之突然,信息公布不及时、管理部门准备不足、医院物资紧缺、社会人心惶惶、捐赠道路进退受阻,无一不体现突发公共事件时管理应急能力的缺失。这场对抗疫情的战役,就是考验管理者的战役。
居安思危的重要性在这个特殊时期得以体现。当前经济环境下,高新科技迅速发展,经济多元化、细分化,全球范围内竞争愈演愈烈。发展企业战略,要求企业积极搏击,把握实际经济环境,准确判断经济大潮,迎接前所未有的市场挑战。
如何提前建立良好的管理机制?
首先必须先设立一个战略目标。
企业没有一个很好的战略管理,就像在迷雾弥漫的大海中没有指南针一样致命。
设立战略目标和制定明确任务的前提是正确识别和评价外部机会。战略目标并非一成不变,它应随着外部竞争环境的变化做适度的调整。不断舍弃该舍弃的,保留或获取该保留和该获取的,这样才能不断提高企业的预测能力,及时准确地作出科学的应对方案。
目前家具行业整体水平不高,利用好这样一个缓冲时间段来进行铺垫。行业整体水平不高是坎,也是机会,它给予企业试错的可能。或者说,当下,就是需要有些企业勇敢地站出来积极试错,并在摸索的过程中,逐渐捋清和完善战略框架。
本次疫情给我们带来了一些启发——家居电商可能迎来再度爆发、移动互联网营销将成为未来重要营销阵地、电商平台、抖音带货火爆,智能家居迎来发展机遇、家庭办公日趋普遍、服务可能比产品更重要等等。广大家具企业应积极面对,调整发展战略方针来以适应本阶段社会经济发展的“新常态”。机遇的风口随时在变化,这一刻的机会没有抓住就只能成为跟风者。
其次是要建立完善明确的标准化体系。
训练有素的军队为什么能在危机情况下做出快速响应,击溃敌人,这全都有赖于平时的标准化训练。一个有效的标准化体系,既可以保障高效的日常生产和工作,同时可以在品质突发事件中快速发现问题所在,帮助企业精准溯源,解决问题;标准体系的建立还可以在像武汉疫情这种不可抗力的影响下,帮助企业最快速恢复生产、最大限度的降低损失。
标准化的实质就是科学化、规范化、经济化。标准化体系,一般包括家具产品标准、家具生产工艺技术标准和家具企业管理标准三个重要组成部分。它能为行业标准化的修订、实施进行规划并提供依据树立标准在家具制造中的标杆作用,并制定应急措施。
这个标准化体系不仅仅包含着产品的设计标准、质量标准,也涵盖了企业的管理标准、采购标准、服务标准,让标准化体系不管在何种突发事件中,标准均能成为整齐划一、快速响应、规范生产、凝集力量的有力武器。
目前,中国家具企业的普遍标准化程度还不高,很多企业对于标准化活动没有主观愿望,更多的是迫于企业眼下的经济效益,被动地去完成最基本的标准工作,并未没有真正意识到标准化的重要性。
标准化工作的开展,是一个相对矛盾体,要在标准成效的短期预期与企业长期的成本投入之间寻求到平衡点。对于现代家具企业而言,可以先尝试根据家具生产销售的每一个环节设立不同的目标,并为实现这些目标,依次建立原材料采购验收标准、设计生产标准、产品质量标准、销售物流标准、售后服务标准等等标准化体系的枝叶。
同时要意识到,标准化体系也绝非一朝一夕所能完成。标准化是一个塑造企业灵魂与价值的过程,也是一个实现科学发展、可持续发展的良性过程。
以标准化为核心才能真正做到以客户、以质量、以经济效益为中心,才能使得企业在风云变幻的市场中处于不败之地占领高点,谋求发展。
能做到“居安思危”的企业才能经受住各种考验,谁也不会知道2020年新春来临之际会有武汉疫情的出现,谁也无法预见2021或者更远的将来会发生什么,我们所能做的是珍惜当前的时光,夯实自己的基础,保持一个居安思危的心态,做到未雨绸缪,积极应对,让企业在波诡云谲的大潮中能够得心应手,游刃有余,可以肯定的是,当危机再次出现,倒下的一定不会是我。
贰
降本升质,主动求变挖掘附加价值
对于家具制造业而言,疫情造成的损失是不可避免的,但企业可通过降本升质在这场无硝烟战争中平缓过渡。
降本——降低制造成本包括直接材料、直接人工和制造费用。
在制造业中,原材料费用占了总成本的很大比重,普遍可达60%,高的甚至超过90%。原材料费用,是成本控制的主要对象。影响原材料成本的因素有采购、库存、材料利用率、质量控制等。目前,材料价格处于一个不可控并持续上升的状态,所以企业应转而考虑在物料的利用率上下更多的功夫。比如,现在很多实木企业的木料利用率都达不到50%,这代表企业花100块钱买的木材,有50块钱是浪费掉的。这意味着企业有非常大的降本空间。